- All
- Gas Treatment
- Oil Treatment
- Produced Water
- Renewable
- Separation
- Utilities
- Water Treatment
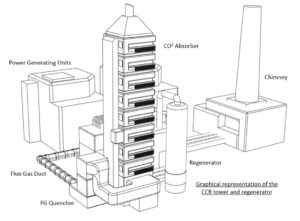
Carbon Dioxide Recovery Facility
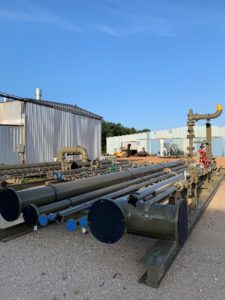
Multi-Well Modules
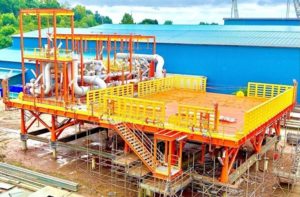
ONGC KG DWN 98/2 FPSO Project
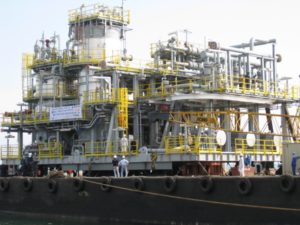
FPSO Ningaloo Vision, Apache Van Gogh Project, Western Australia
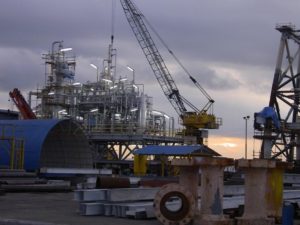
Baobab FPSO, Cote d’Ivoire, West Africa
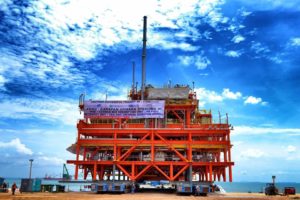
Husky Madura FPSO
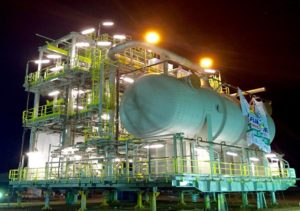
ENI – OCTP – GHANA
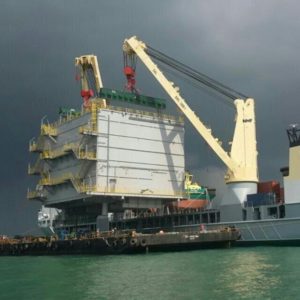
Petrobras P-74 Cessao Onerosa FPSO – E-House
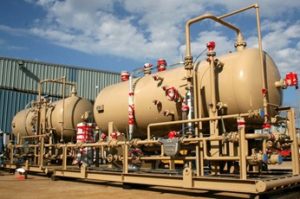
Three Phase Separator Program
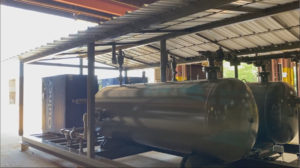
Facility Program Orders – Major WTX Producer
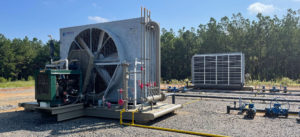
Electric & Natural Gas Coolers
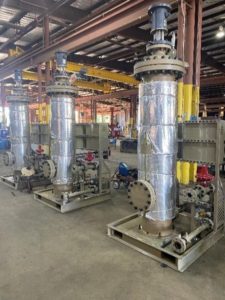
Standard O2 Recovery Units
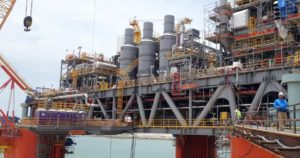
Delta House FPS
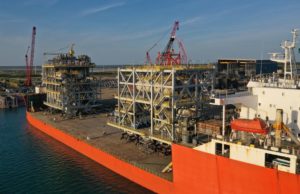
ENI Mexico Area 1 FPSO Project
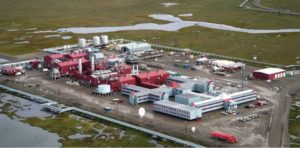
Milne Point Alaska
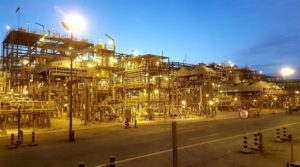
Wasit MEG Regeneration & Reclamation
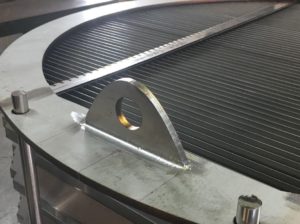
Food and Beverage Process Optimization
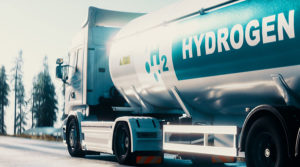
Liquid Hydrogen Electrolyzer Building Study
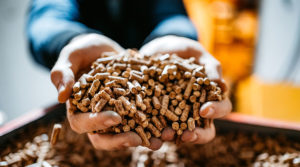
Transportation Fuels from Biomass
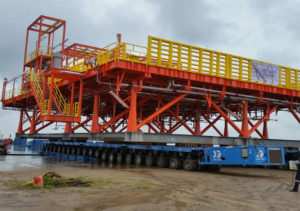
ONGC KG DWN 98/2
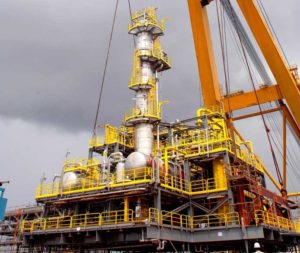
Cachalote Relocation of FPSO Capixaba
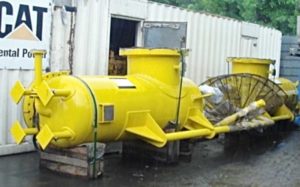
ENI Block 15/06 West Hub FPSO
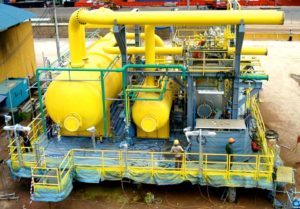
Generic Gas FPSO 1, Cidade De Sao Mateus, Brazil
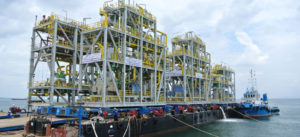
FPSO Cidade de Mangaratiba MV24
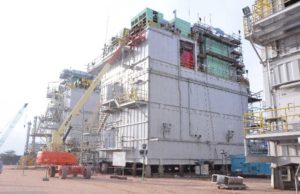
P61 Offshore Substation and Electrical Equipment
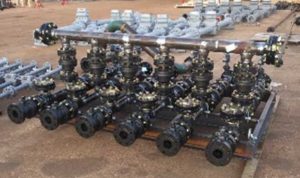
ESP Multi-Well Manifolds
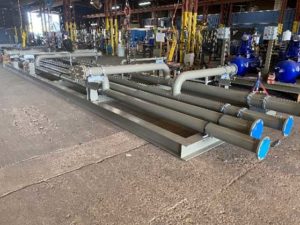
Central Processing Pipe Modules
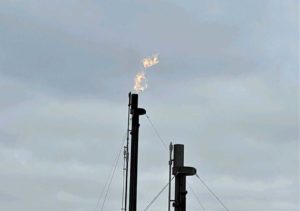
Flare Gas Recovery
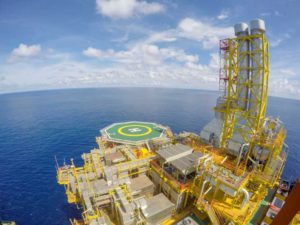
Kings Quay FPS
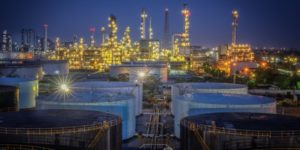
Nassiriyah Degassing Station
